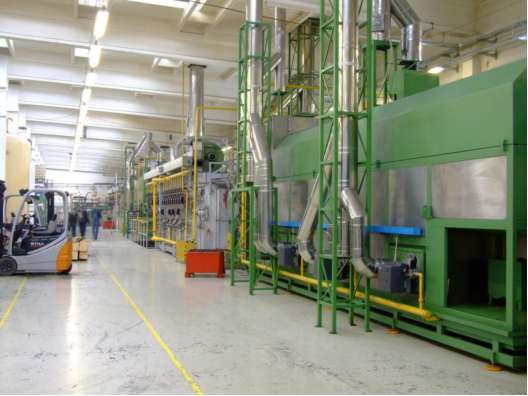
Are you looking for an easy way to improve efficiency and reduce mistakes on the shop floor?
One Point Lessons could be the solution you need. These simple, visual employee training tools focus on a single task or process, making it easier for workers to learn and apply key skills quickly.
In this article, we’ll show you how One Point Lessons can boost productivity, improve safety, and create a more streamlined work environment-helping your team perform at its best.
Why Use One Point Lessons in Manufacturing?
One Point Lessons help improve the manufacturing efficiency of workers by providing clear instructions. This reduces the time needed for training and helps employees perform tasks more quickly. When workers understand their tasks well, it also reduces the chances of making mistakes.
Safety is another key reason to use OPLs in manufacturing. They can clearly explain safety protocols, ensuring that workers follow proper procedures. This helps reduce accidents and keeps the workplace safe for everyone.
OPLs can also be used to reinforce the concept of takt time, ensuring that workers understand the rhythm of production to meet demand efficiently. By incorporating takt time, OPLs help maintain smooth workflow and avoid delays.
Creating Effective One Point Lessons
Start by choosing a specific topic for the One Point Lesson. The topic should focus on an important task or process that workers regularly perform. Avoid broad subjects, as it is best to focus on a single point of interest.
Next, simplify the information to make it easy to understand. Use clear, direct language and focus only on the essential steps or facts. Add visual aids like diagrams or pictures to enhance the clarity of the lesson.
Examples of One Point Lessons in Manufacturing
One example of an OPL could be instructions on how to operate a machine. It might include steps for setting up the machine, loading materials, and checking settings. This ensures that operators know the correct way to run the equipment safely.
Another example could be a lesson on quality control checks. It might describe the steps to inspect a product for defects and record the results. The lesson would help workers maintain consistent quality in production.
Best Practices for Using One Point Lessons
Involve employees in creating One Point Lessons for more practical and relevant lessons. Workers who do the tasks regularly can provide insights into the best way to explain the process. This increases the chances that the lesson will be effective.
Regularly update One Point Lessons to keep them relevant. As processes change or improve, OPLs should be revised to reflect the new methods. This ensures that the lessons remain useful and accurate for the workers.
Unlock Efficiency With One Point Lessons on the Shop Floor
One Point Lessons are an effective tool to improve training and efficiency on the shop floor. They offer a simple, clear way to communicate important tasks and procedures. By making information easy to understand and access, workers can perform their duties with more confidence and accuracy.
Using these lessons regularly helps create a safer and more productive work environment. They ensure that employees are always equipped with the knowledge they need to succeed.
Were you satisfied with the information in this article? If yes, our blog offers even more valuable resources.