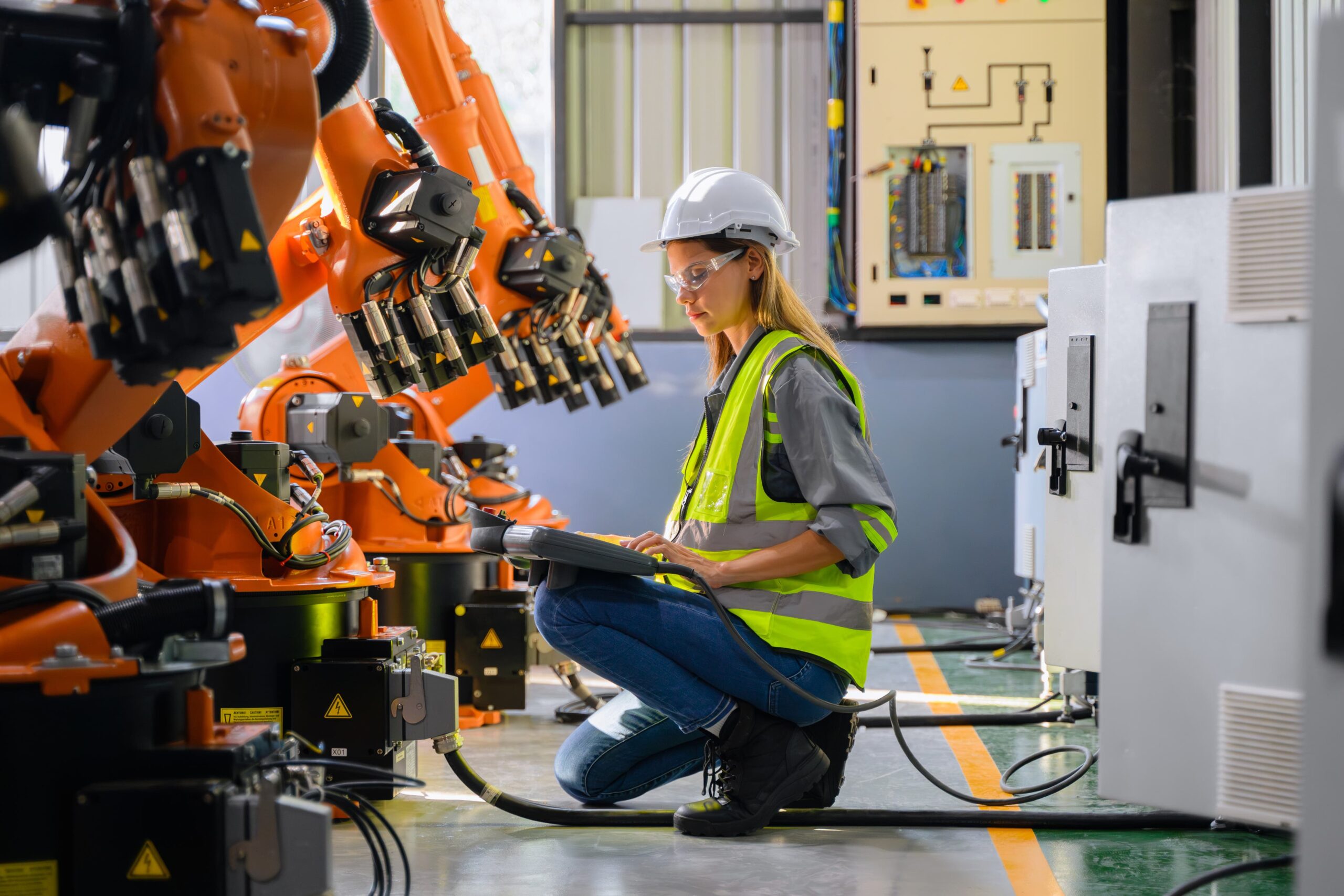
The 21st century’s business environment is competitive, so companies like Alcatel-Lucent Enterprise are constantly looking for ways to improve production profitability. To have a cutting edge in competition businesses must embrace the mainstay of the industrial revolution.
This approach changes traditional assembly lines completely by using advanced technologies such as IoT, IIoT, AI, big data analytics, robotics and automation.
Contents
What is Smart Manufacturing and Why Does It Matter?
Smart manufacturing is a revolutionary strategy transforming the production industry. It employs advanced technology (including software and hardware), automation and data analytics to decrease costs, increase revenues and reduce defects in production. When compared to other methods, this is an efficient way that reduces down time since it takes into account costs as well as efficiency.
This technique leads to greater productivity, efficiency, and safety. By automating dangerous or repetitive tasks that can be automated in order to free up employees for work that requires human intervention; however. Automation may perform tedious or dangerous functions freeing human workers to engage in more complex creative activities which lead to enterprise innovation as well as improvement.
Advantages of Implementing Smart Manufacturing
Here are some benefits of integrating smart manufacturing into your business:
IoT and IIoT Networks: Enhanced connectivity between devices ensures constant flow of data with real-time insights about production processes leading to optimization at all points within the manufacturing process making it able to respond quickly when issues arise.
5G Connectivity: The ability for high-speed communication is crucial for swift data transmission which allows real-time decision-making thus increasing responsiveness in operations.
Real-time Monitoring and Data Collection: Immediate processing of data and its analysis, thus providing useful insight that can be used to optimize operations, predict maintenance needs and improve overall efficiency.
AI and Machine Learning: Advanced data-driven insights and automation enhance the ability to make informed decisions and improve processes continuously. Predictive maintenance is one use for this technology as well as quality control or optimizing supply chain.
Robotics and Automation: The precision in their operation makes manual labor unnecessary while speeding up production and ensuring consistency. Robots are more precise therefore they make fewer mistakes, which improves the quality of products.
Cyber-physical Systems (CPS): Combining physical systems with computational ones enables interactions between digital components of a manufacturing process. This allows for real-time monitoring and control over physical processes by increasing their efficiency hence reducing downtime.
Digital Twin Technology: Testing and refining production methods through simulation without interrupting them reduces risks posed during the implementation process.
Advanced Materials and Additive Manufacturing: Streamlined production with reduced waste along with improved efficiency results in cost savings as well as environmental benefits. 3D printing also known as additive manufacturing produces complex parts which generate minimal waste.
Cloud Computing: Scalable resources for data management remote collaboration help enterprises to respond quickly to changing business imperatives, utilize global skills banks among others.
Why Smart Manufacturing Is Important
Smart manufacturing improves the efficiency of business operations, such as production time, quality, and internal responsiveness. The smart factory is more adaptable and flexible than a traditional factory, enabling quick adjustments to changing consumer expectations or market conditions. In today’s highly competitive market where consumer demands and technological advancements are constantly developing at a fast pace, this adaptability is vital.
Optimizing Production Processes with Smart Manufacturing
Smart manufacturing optimizes production processes through various methods that will future-proof it:
Predictive Maintenance: Through data analysis of IoT/IIoT and AI sensors’ equipment condition monitoring which allows for cost-effective real-time maintenance. This technique minimizes downtime and maintenance costs by addressing problems before they result in machine failure.
Supply Chain Optimization: This provides data visibility across operations creating an intelligent connected supply chain. Such optimization makes inventory management more efficient, reducing lead times and increasing customer satisfaction.
Quality Assurance (QA 4.0): AI being involved in advanced automated inspections ensures that consistent product quality is maintained through the use of machine learning techniques on random inspection samples only instead of testing all products produced by a given process . When compared to manual inspections, automated quality assurance eliminates defects thereby ensuring high standards for goods before they reach customers.
Worker Safety: It uses state-of-the-art detection systems plus real-time monitoring to detect hazards making workplaces safer environments.Safe work environment can be ensured by use of safety features like sensors and automatic responses which could prevent accidents or protect workers from hazardous environments.
Additional Benefits
Digital Workflows: Streamlined processes as well as efficient operations cut down the time and effort required to complete tasks thus leading to shorter production cycles coupled with lowered operating expenses.
Autonomous Intralogistics: Factory internal logistics automation minimizes material flow delays increasing its efficiency within the facility.
Robotics Material Handling: Efficiently managing materials reduces waste and ensures that resources are used in the company, which results in cost savings and environmental benefits.
Augment-ready Workforce: Employees can become more productive, safer, and happier at their jobs by improving their skills using advanced tools. It also helps them work better due to improved training programs hence increasing productivity.
Final Thoughts
The fast-paced 21st century demands constant changes to be made in the manufacturing industry. Many advantages including ease of operation, safety of employees, sustainability and resource conservation have been attributed to smart manufacturing. It enables businesses scale efficiently while optimizing production quality or retaining equipment. Industry 4.0 employs the latest technologies such as AI and machine learning for process simplification as well as improvement.
Start transforming your business today. To implement smart manufacturing systems in your factory or plant, contact Alcatel-Lucent Enterprise.Click here to schedule a demo.