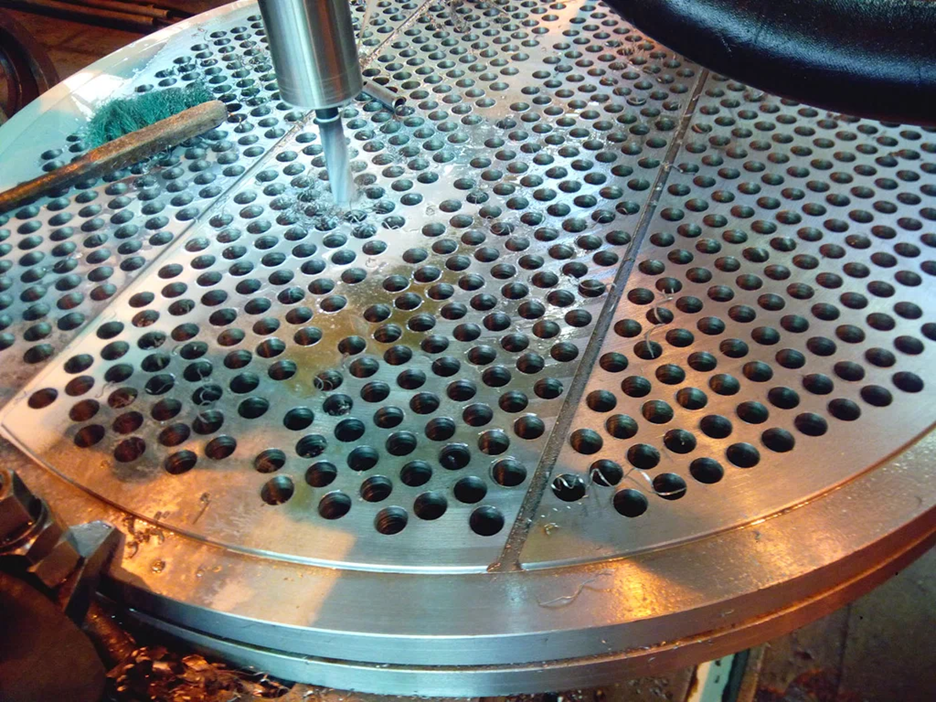
The manufacturing world has made incredible strides thanks to technologies that allow the production of complex materials at industrial scales. One such marvel is the hollow fiber spinning machine. These machines are critical for creating hollow fibers, tiny tubular structures that play a crucial role in fields such as medical treatment, water purification, and gas separation. As industries continue to innovate, the demand for reliable, high-quality hollow fiber spinning equipment only grows.
What is a Hollow Fiber Spinning Machine?
A hollow fiber spinning machine is a specialized device used to produce fibers with a hollow core. Unlike solid fibers, hollow fibers have a central channel that makes them lightweight, flexible, and highly efficient for filtration and transport applications. The machine extrudes a polymer solution around a bore fluid through a spinneret, forming fibers that are solidified in a controlled environment to retain their hollow shape. This process requires precise control over material flow, temperature, and other critical parameters to ensure consistent fiber quality.
How Hollow Fiber Spinning Works
The spinning process typically involves extruding a polymer solution through a specialized spinneret while simultaneously injecting a bore fluid that creates the hollow center. The emerging filament is then passed through an air gap and into a coagulation bath where it solidifies. Post-solidification, the fibers are stretched, washed, and dried before being collected onto spools.
The entire system must operate with incredible precision. Even slight variations in flow rate, temperature, or chemical composition can lead to fibers with poor mechanical properties or inconsistent internal diameters, which can critically affect their performance in end-use applications.
Components of a Hollow Fiber Spinning Machine
Several key components come together to produce high-quality hollow fibers:
Polymer Delivery System
This system controls the supply of polymer solution to the spinneret. High-pressure pumps and precision flow meters ensure that the polymer is fed at a consistent rate, which is vital for maintaining fiber uniformity.
Spinneret Design
The spinneret is a core component where the polymer solution and bore fluid meet. It features a specialized configuration to simultaneously extrude the outer polymer while forming the inner hollow structure. The precision of the spinneret design directly influences fiber dimensions and consistency.
Coagulation Bath and Air Gap
Depending on the type of spinning, an air gap may be present between the spinneret and the coagulation bath. The bath typically contains a non-solvent that triggers the polymer to solidify. Control over the bath’s temperature and composition is essential to create defect-free fibers.
Fiber Drawing and Collection
After formation, fibers are drawn through a series of rollers that stretch and align the polymer chains, improving mechanical strength. Finally, the fibers are collected onto spools in a controlled manner to prevent damage or entanglement.
Types of Hollow Fiber Spinning Machines
Different spinning techniques are employed depending on the end-use requirements:
Dry Spinning
In dry spinning, the polymer solution is extruded into a heated gas environment where the solvent evaporates. This method is suitable for polymers sensitive to liquid coagulation.
Wet Spinning
In wet spinning, fibers are extruded directly into a liquid coagulation bath. This is the most traditional method and is ideal for polymers that cannot tolerate air drying.
Dry-Wet Spinning
Dry-wet spinning combines elements of both methods, with an air gap followed by a coagulation bath. This technique allows for greater control over fiber morphology and is commonly used for high-performance applications like membrane production.
Applications of Hollow Fiber Spinning Machines
Hollow fibers produced by these machines serve a wide range of critical functions:
Water Filtration Systems
Hollow fiber membranes are the backbone of modern water filtration systems, including microfiltration, ultrafiltration, and reverse osmosis units. Their high surface area-to-volume ratio and durability make them ideal for removing contaminants from water.
Medical Applications
In healthcare, hollow fibers are used in hemodialysis membranes, artificial lungs, and drug delivery systems. Their ability to selectively filter molecules based on size is vital for safe and effective patient treatment.
Gas Separation Processes
Industries use hollow fiber membranes for gas separation tasks, such as enriching oxygen from air or removing carbon dioxide from natural gas streams. These processes rely on the fiber’s permeability and selectivity, properties that stem from the spinning machine’s precision.
Challenges in Hollow Fiber Spinning
Despite its advantages, hollow fiber spinning comes with several challenges:
- Material Sensitivity: Some polymers are difficult to process, requiring stringent environmental controls.
- Defect Management: Tiny defects like pinholes can drastically affect fiber performance.
- Complexity of Scale-up: Moving from laboratory-scale spinning to mass production demands sophisticated machine design and process optimization.
Constant attention to process parameters and regular maintenance of the machinery are necessary to mitigate these issues.
Innovations and Future Trends
The future of hollow fiber spinning technology is geared toward automation, sustainability, and smarter materials:
- AI Integration: New machines are being developed with AI-driven process monitoring that adjusts conditions in real-time to prevent defects.
- Eco-friendly Production: Efforts are underway to develop solvent-free or low-solvent spinning methods.
- Advanced Membrane Materials: Nanotechnology is helping create fibers with unprecedented properties, such as increased permeability and chemical resistance.
These innovations promise to expand the range of applications for hollow fibers even further while reducing the environmental footprint of their production.
Conclusion
A hollow fiber spinning machine is far more than just a piece of industrial equipment; it is a gateway to creating products that touch nearly every aspect of modern life. From delivering clean drinking water to saving lives in hospitals, the fibers produced by these machines are indispensable. As technology advances, hollow fiber spinning machines will continue to evolve, offering greater precision, higher efficiency, and broader application possibilities in a rapidly changing world.