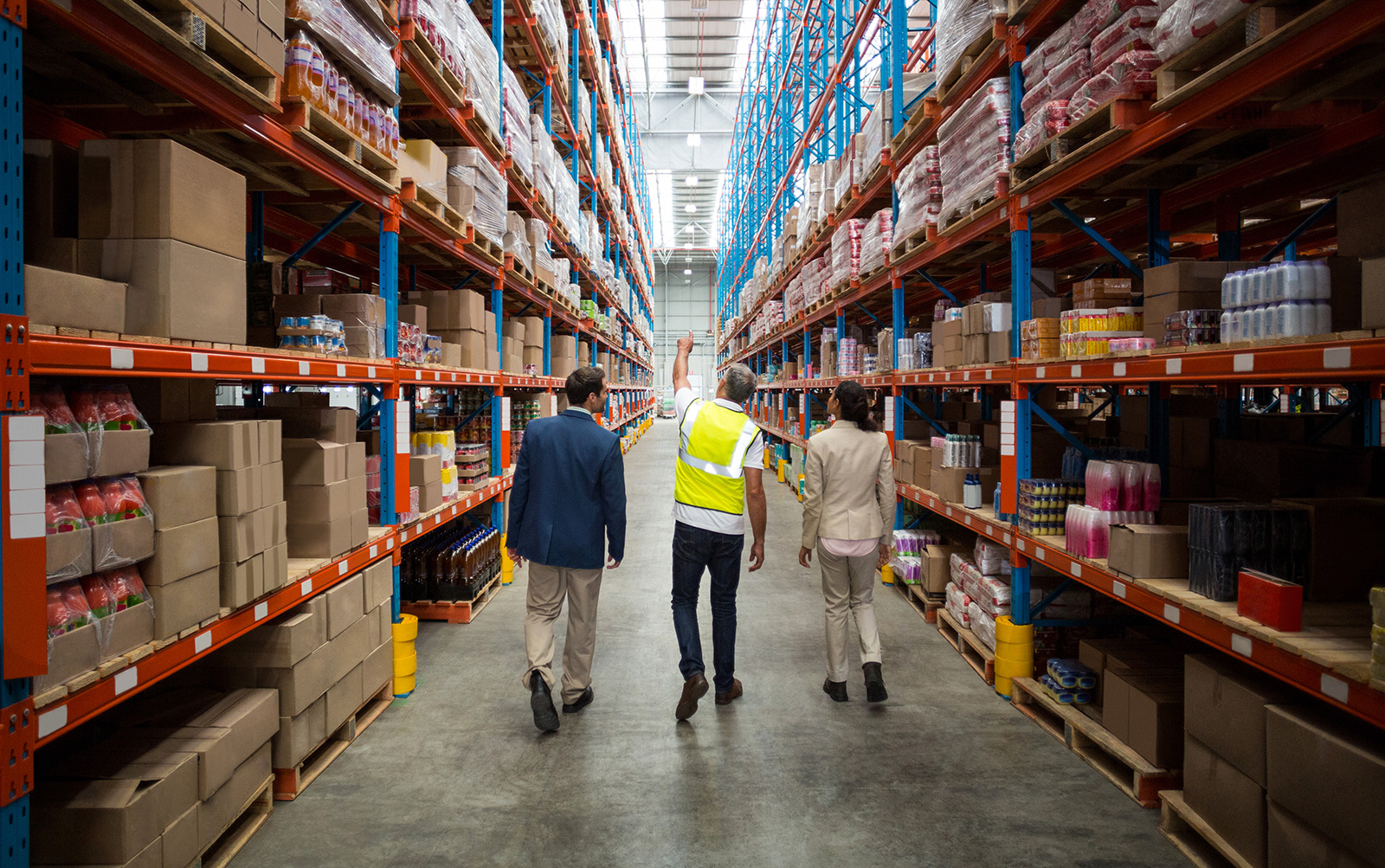
In today’s fast-paced business environment, warehouse efficiency is crucial for maintaining a competitive edge. As companies strive to meet increasing customer demands and optimize their supply chain operations, implementing effective strategies to enhance warehouse productivity becomes paramount. This article explores the top five strategies for boosting warehouse efficiency, providing insights that can revolutionize your operations and drive success.
Contents
- 1 1. Implement Advanced Warehouse Management Systems (WMS)
- 2 2. Optimize Warehouse Layout and Storage Systems
- 3 3. Embrace Automation and Robotics
- 4 4. Implement Lean Warehouse Practices
- 5 5. Invest in Employee Training and Engagement
- 6 6. Textile Production Tracking for Your Global Supply Chain
- 7 Conclusion
1. Implement Advanced Warehouse Management Systems (WMS)
One of the most impactful strategies for increasing warehouse efficiency is the implementation of a robust Warehouse Management System (WMS). A WMS provides real-time visibility into inventory levels, order status, and warehouse operations, enabling better decision-making and resource allocation. With features like automated data collection, inventory tracking, and order processing, a WMS can significantly reduce errors and streamline workflows.
Advanced WMS solutions, such as those offered by Modula in Australia and New Zealand, integrate seamlessly with other business systems, providing a comprehensive view of the entire supply chain. These systems can optimize picking routes, manage labor effectively, and provide valuable analytics for continuous improvement. By leveraging the power of data and automation, warehouses can achieve higher accuracy rates, faster order fulfillment, and improved overall efficiency.
2. Optimize Warehouse Layout and Storage Systems
The physical layout of your warehouse plays a crucial role in its efficiency. A well-designed layout minimizes unnecessary movement, reduces picking times, and maximizes storage capacity. To optimize your warehouse layout, consider implementing a logical flow that supports a smooth, sequential process from receiving to shipping. Utilize vertical space by employing high-density storage solutions like vertical lift modules or multi-level racking systems to maximize floor space. Create dedicated zones for different activities such as receiving, picking, packing, and shipping to minimize congestion and improve workflow. Additionally, implement a slotting strategy by placing fast-moving items in easily accessible locations to reduce travel time and increase picking efficiency.
By carefully analyzing your inventory and order patterns, you can create a layout that supports efficient operations and adapts to changing business needs.
3. Embrace Automation and Robotics
Automation and robotics are revolutionizing warehouse operations, offering unprecedented levels of efficiency and accuracy. From automated guided vehicles (AGVs) to robotic picking systems, these technologies can dramatically improve productivity while reducing labor costs and human error. Consider implementing automated storage and retrieval systems (AS/RS) that can quickly and accurately retrieve items from storage, significantly reducing picking times. Automated conveyor systems can efficiently move products through the warehouse, reducing manual handling and improving throughput. Advanced robots can handle repetitive tasks with high precision, freeing up human workers for more complex activities. Additionally, drones equipped with scanners can perform inventory counts quickly and accurately, even in hard-to-reach areas.
While the initial investment in automation can be significant, the long-term benefits in terms of efficiency, accuracy, and scalability often justify the cost.
4. Implement Lean Warehouse Practices
Lean principles, originally developed for manufacturing, can be highly effective when applied to warehouse operations. The goal of lean warehousing is to eliminate waste, improve flow, and add value to the customer. Key lean practices for warehouses include the 5S methodology: Sort, Set in order, Shine, Standardize, and Sustain to create a clean, organized workspace that promotes efficiency. Value stream mapping can be used to analyze and optimize the flow of materials and information through your warehouse. Continuous improvement (Kaizen) encourages employees to identify and implement small, incremental improvements in their daily work. Just-in-time (JIT) inventory practices help minimize excess inventory by aligning stock levels with actual demand.
By adopting lean practices, warehouses can reduce waste, improve space utilization, and enhance overall operational efficiency.
5. Invest in Employee Training and Engagement
While technology and processes are crucial, the human element remains a key factor in warehouse efficiency. Well-trained, motivated employees are essential for implementing and maintaining efficient warehouse operations. Consider implementing comprehensive training programs to ensure all employees are thoroughly trained on warehouse processes, safety procedures, and the use of technology. Cross-training enables employees to perform multiple roles, increasing flexibility and reducing bottlenecks. Implementing clear performance metrics and reward systems can motivate employees and drive productivity. Encouraging employees to share ideas for improving processes and efficiency fosters a culture of continuous improvement.
By investing in your workforce, you create a culture of efficiency and continuous improvement that can drive long-term success in your warehouse operations.
6. Textile Production Tracking for Your Global Supply Chain
Effective textile production tracking is crucial for managing a global supply chain in today’s fast-paced market. Our Track IT software provides real-time visibility into every production stage, from raw material sourcing to finished goods. With features like barcode scanning and inventory management, you can monitor stock levels, track order progress, and ensure timely deliveries. This not only minimizes delays but also enhances communication with suppliers and partners. By leveraging data analytics, TRACKIT helps you make informed decisions, reduce waste, and improve overall efficiency in your textile operations. Streamline your supply chain and boost competitiveness with our advanced Textile tracking solutions.
Conclusion
Improving warehouse efficiency is an ongoing process that requires a multifaceted approach. By implementing advanced warehouse management systems, optimizing layout and storage, embracing automation, adopting lean practices, and investing in your workforce, you can significantly enhance your warehouse’s productivity and competitiveness. As the business landscape continues to evolve, warehouses that prioritize efficiency will be best positioned to meet the challenges of tomorrow and deliver exceptional value to their customers.