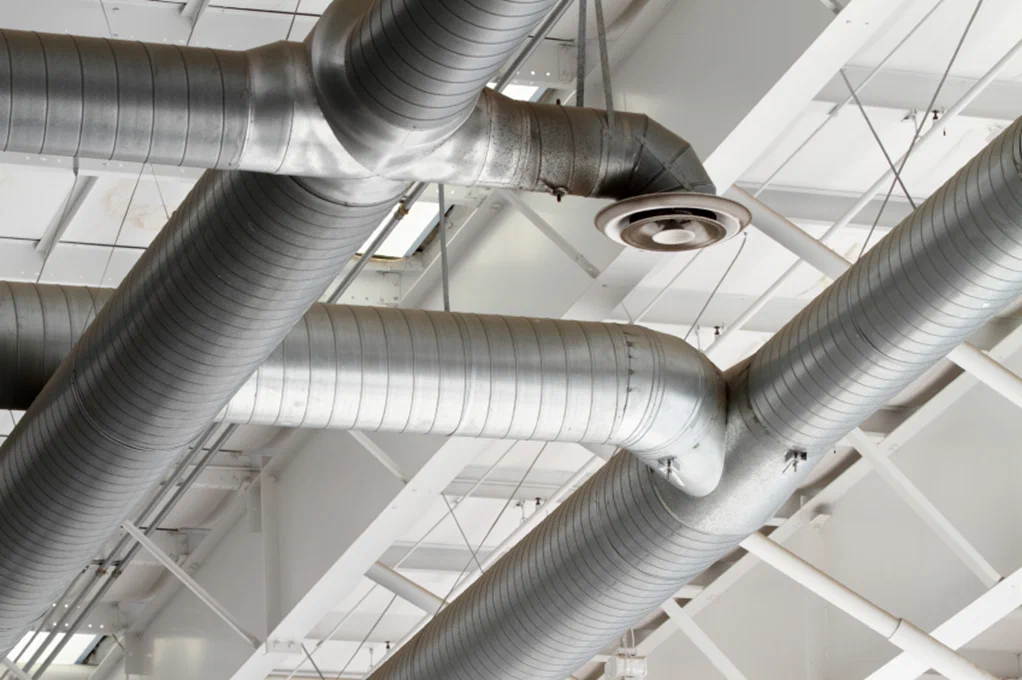
Ventilation in deep mines is more than a necessity—it’s a lifeline. Underground mining ventilation systems ensure that workers have access to fresh air while effectively removing hazardous gases, dust, and heat. Without well-designed ventilation systems, the safety of mining teams, operational efficiency, and environmental standards are at risk.
This article dives into the challenges of designing effective ventilation systems in deep mines, explores the factors affecting their performance, and highlights innovative solutions and best practices. We’ll also touch on fascinating case studies that demonstrate successful implementations and what the future holds for mine ventilation.
Contents
Why Proper Ventilation Matters in Deep Mines
Deep mines present unique and hazardous working conditions. At greater depths, the Earth’s natural geothermal gradients cause rising temperatures, making it uncomfortable—even dangerous—for workers. Harmful gases like methane and carbon dioxide, along with airborne pollutants such as dust and diesel exhaust, can accumulate in poorly ventilated areas.
Properly designed underground mining ventilation systems are critical for mitigating these risks. They ensure fresh air continuously circulates, reduce heat and humidity levels, and remove contaminants from the air, enabling safer, more productive working conditions.
Key Challenges in Ventilation System Design
Designing ventilation systems for deep mines is no small feat due to several inherent challenges. Here’s a look at some of the most common obstacles that mining engineers and environmental consultants face:
- Depth and Size of the Mine
Deep mines stretch kilometers below the surface, making it exceptionally challenging to deliver sufficient airflow throughout. Larger mine depths require higher energy inputs and advanced technologies to push fresh air where it’s needed.
- Heat and Humidity Issues
At extreme depths, heat from the Earth’s core and mining machinery can significantly raise temperatures, often crossing 40°C. Humidity levels can soar due to groundwater infiltration, resulting in severe discomfort for workers and increased equipment maintenance needs.
- Toxic Gas Control
Natural deposits of methane or carbon monoxide, along with exhaust emissions from mining equipment, pose severe health hazards. Ensuring their removal without introducing additional contaminants is critical.
- High Energy Consumption
Ventilation systems are notoriously energy-intensive to operate, often representing up to 50% of a mine’s total energy costs. Balancing effective ventilation with energy efficiency remains a top concern for engineers.
- System Durability
The harsh underground environment can degrade system components like fans, ducts, and air conditioning units reducing the efficiency and lifespan of ventilation infrastructure.
- Environmental Compliance
Increasingly stringent environmental regulations have placed additional responsibilities on mining companies to minimize greenhouse gas emissions, sustainable energy use, and other environmental impacts.
Factors Affecting Ventilation Efficiency
Several factors influence how well underground mining ventilation systems perform. These include the mine’s layout, airflow distribution, and operating conditions.
- Mine Layout: The size, shape, and number of working areas in the mine play a crucial role in determining airflow requirements and equipment placement.
- Air Quality Monitoring: Efficient systems incorporate real-time sensors to measure toxic gases and optimize airflow. Without this, maintaining air quality can be a guessing game.
- Fan Efficiency: The selection of high-quality, energy-efficient fans and proper placement within the mine are key to driving adequate airflow.
- Leakages: Duct leakages, often caused by wear and tear or poor installation, can waste energy and compromise air delivery to critical areas.
Innovative Solutions and Best Practices
To overcome these challenges, Mechvac engineering and safety experts have developed innovative solutions that optimize ventilation performance while maintaining cost efficiency.
- Advanced Software for Airflow Modeling
Modern computational fluid dynamics (CFD) software allows engineers to simulate how air moves through a mine, enabling them to predict problem areas and optimize system designs.
- Variable Speed Control Fans
Instead of running fans at constant speeds, variable speed control technology allows airflow to be adjusted based on real-time demand, reducing energy costs while maintaining sufficient ventilation.
- Thermal Insulation and Water Sprays
Insulating mining equipment or using water spray systems helps combat heat buildup, ensuring a more comfortable working environment.
- Integration with Renewable Energy Sources
Mining operations are increasingly turning to renewable energy to power their ventilation systems, reducing environmental footprints and operational costs over time.
- Regular Maintenance Schedules
Routine inspections and maintenance of ventilation components help prevent leakages, optimize efficiency, and extend system lifespans.
The Future of Ventilation in Deep Mines
Looking ahead, the future of underground mining ventilation systems lies in the integration of cutting-edge technologies and sustainability practices.
- Automation and AI: AI-driven algorithms will optimize airflow in real-time while predicting irregularities such as equipment failures or gas buildups.
- Green Energy Integration: More mines will adopt energy-efficient systems powered by wind, solar, or geothermal energy.
- Smart Ventilation Networks: IoT devices and smarter sensors will allow dynamic system adjustments, ensuring maximum effectiveness at minimal energy costs.
Such advancements will not only enhance mine safety but also help operators meet their environmental stewardship goals while maintaining profitability.
Conclusion
Deep mining poses countless challenges, but proper ventilation design ensures safety, compliance with regulations, and operational efficiency. While the complexities may seem daunting, advancements in technology and innovative engineering have made significant strides in overcoming these challenges.